張維合,馮婧,趙利平,胥永林,閆麗靜,費強,陶永杰,陳卓航
(廣東科技學院,廣東東莞523000)
摘要:針對汽車左前門板的尺寸大小、結(jié)構(gòu)特點和工藝要求,設計了一副大型薄壁順序閥控制的熱流道注塑模具。模具喇叭網(wǎng)孔成型零件采用粉末冶金透氣鋼,有效消除了喇叭網(wǎng)孔中填充不良和熔接痕等成型缺陷。模具采用傾斜式導滑槽,有效解決了傾斜式內(nèi)側(cè)倒扣脫模難題。模具采用由順序閥智能技術(shù)控制的熱流道澆注系統(tǒng),有效解決了汽車左前門板尺寸大壁厚小熔體填充難題。模具采用快速且均衡溫度控制系統(tǒng),注射周期縮短了約8%,尺寸精度達到了MT3(GB/T14486—2008)。
關(guān)鍵詞:汽車左前門板;大型注塑模具;順序閥熱流道;側(cè)向抽芯機構(gòu)
前言
汽車門板是汽車內(nèi)飾件的重要組成部分,位于汽車車門的內(nèi)側(cè)。為因應輕量化、美觀化和安全性要求,汽車門板都采用塑料,由注塑模具注射成型。汽車門板批量大,尺寸大,結(jié)構(gòu)復雜,汽車門板注塑模具是典型的大型、薄壁、精密、復雜且長壽命注塑模具,設計難度大,設計周期長。本文介紹了某款新能源汽車左前門板注塑模具的先進結(jié)構(gòu)及其創(chuàng)新技術(shù)。
1 塑件結(jié)構(gòu)及成型工藝要求
圖1所示為某款新能源汽車左前門板零件圖,材料為PP/EPDM,收縮率取1.1%[1],其中EPDM乙烯、丙烯和少量的非共軛二烯烴的共聚物,是乙丙橡膠的一種,能夠提高門板的抗沖擊彈性[2]。塑件結(jié)構(gòu)特點和成型工藝要求如下:(1)塑件尺寸為:804.8mm×721.3mm×102.4mm,平均壁厚2.6mm,流長比約為200,為典型的大型薄壁塑件,成型困難。(2)塑件外形復雜,塑件內(nèi)、外側(cè)面共有S1~S6共6個與脫模方向不一致的倒扣,脫模困難。(3)塑件外觀面(俗稱A面)蝕皮紋,脫模斜度均大于或等于5°(4)基于車門的位置,成型塑件外觀面不允許有飛邊、收縮凹陷、熔接痕等缺陷,也不允許有黑斑和點澆口痕跡。
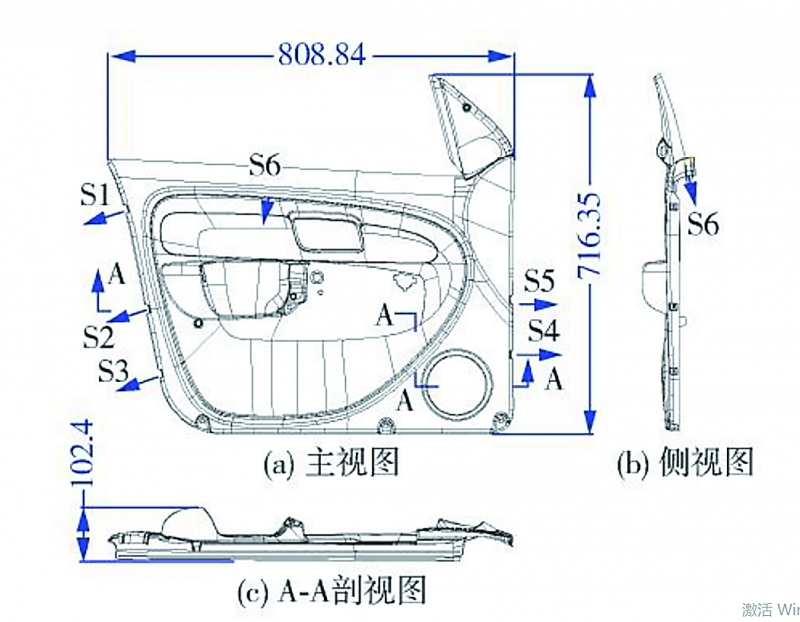
圖1 汽車左前門板零件圖
2 模具結(jié)構(gòu)設計
由于汽車左前門板屬于大型平板類零件,為改善熔體填充,模具采用熱流道澆注系統(tǒng),但由于塑件表面不允許有澆口痕跡,塑料熔體最后由扇形澆口從側(cè)面進入模具型腔。塑件內(nèi)外側(cè)面共有6個倒扣,其中S6為內(nèi)側(cè),倒扣面積大,倒扣深度10mm,模具中采用“斜頂+斜推桿”的內(nèi)側(cè)向抽芯機構(gòu);S1、S2、S3、S4、S5為外側(cè)倒扣,模具采用“滑塊十斜導柱”抽芯結(jié)構(gòu)。模具詳細結(jié)構(gòu)見圖2。
1—定模固定板2—框板3—定模A板4—定模鑲件5—熱流道板6—二級熱射嘴
7一定位圈8—一級熱射嘴9—動模B板10—限位柱11—推件固定板12—推件底板
13—動模固定板14—方鐵15—推桿16—撐柱17—行程開關(guān)18—頂出油缸19—滑塊
20—擋塊21—鎖緊塊22—斜導柱23—動模鑲件24—導柱25—滾珠導套26—復位桿
27一彈力膠28—耐壓硬塊29—斜導柱30—滑塊31—鎖緊塊32—擋銷33—彈簧
34—耐磨塊35—流道拉桿36—塑件推桿37一斜頂38一斜推桿導套39—斜推桿
40—推件板導柱41—導套42—支撐柱43—斜推桿底座
圖2 汽車左前門板注塑模具結(jié)構(gòu)圖
本模具外形尺寸為:1400mm×13000mm×995mm,總質(zhì)量約10t,屬于超大型注塑模具[3]。
2.1 模具成型零件設計
為提高模具剛度,減小模具的外形尺寸,模具定、動模成型零件與模板采用一體式結(jié)構(gòu),即型腔直接開在定模A板和動模B板上,定模A板選用P20模具鋼,動模B板選用718模具鋼[4]。模具定模A板和動模B板采用四面圍邊的錐面定位結(jié)構(gòu),詳見圖3模具立體圖。
本模具成型零件設計的難點是門板喇叭網(wǎng)孔成型結(jié)構(gòu)的設計。由于喇叭網(wǎng)孔數(shù)量多,模具設計圖中若全部畫出會嚴重影響電腦運行速度,因此門板喇叭網(wǎng)孔設計時,不要在3D上面把每一個喇叭網(wǎng)孔都設計出來,只需要設計少部分的參考喇叭網(wǎng)孔,再在零件上面設計上不同顏色的喇叭網(wǎng)孔分布線,以2D線條來表示喇叭網(wǎng)孔的分布,見圖4。
本例以碰穿網(wǎng)孔的高度為基準,長鋼料封膠,在局部切出幾個喇叭網(wǎng)孔作為網(wǎng)孔尺寸基準進行設計。如果碰穿網(wǎng)孔或者不碰穿網(wǎng)孔都不等高,那么我們需對所有不同高度的網(wǎng)孔都進行3D真實建模。這種設計方法只針對圓形網(wǎng)孔,其他形狀網(wǎng)孔需3D真實建模。碰穿與不碰穿的網(wǎng)孔在3D設計時要有區(qū)分,用顏色區(qū)分最好,見圖5。由于碰穿孔對塑料熔體阻力大,喇叭網(wǎng)孔附近要設計澆口,以改善熔體填充,提高保壓效果,消除熔接痕,見圖6。汽車門板喇叭網(wǎng)孔定模型腔脫模斜度應盡量大,定、動模對碰處要設計0.1~0.15mm臺階(見圖7),動模對應位置應設計加強筋骨防止黏定模。
為避免困氣,喇叭網(wǎng)孔鑲件采用粉末冶金透氣鋼。透氣鋼雖然貴,但排氣效果好。如果采用P20模具鋼,需要在網(wǎng)孔鑲件上設計排氣針或者鑲針,網(wǎng)孔鑲件底部還要設計排氣槽,但這種排氣槽很容易被膠粉和油污堵塞,導致排氣不暢而影響熔體填充,由此造成的損失會生產(chǎn)成本更高[5]。
2.2 模具導向定位系統(tǒng)設計
模具導向定位系統(tǒng)攸關(guān)大型、精密和長壽命注塑模具設計的成敗。汽車左前門板注塑模具設計了4支圓導柱和4支方導柱,其中圓導柱布置在模具的4個角上,尺寸為φ80mm×300mm。方導柱布置在模具4個邊的中間位置,尺寸為50mm×150mm×300mm。方導柱既起導向作用又起定位作用,詳見圖2和圖3。4支圓導柱和四支方導柱都裝配在定模A板上,這種結(jié)構(gòu)既方便成型塑件取出,又方便模具制造,在配模時4支導柱還可作為支撐腳用[6]。
在五組“滑塊+斜導柱”的側(cè)向抽芯機構(gòu)中,每個滑塊都由鎖緊塊推回復位,為減小鎖緊面之間的磨損,導柱24必須在各鎖緊面接觸之前20mm就插入滾珠導套25內(nèi)。
2.3 模具澆注系統(tǒng)設計
針對左前門板為大型、復雜、薄壁平板類塑件,且喇叭網(wǎng)通孔多的特點,模具采用“3點熱射嘴+熱流道板”的澆注系統(tǒng)。3點進料勢必產(chǎn)生多條熔接痕,熔接痕不但影響美觀,也會減小門板的強度。為了消除熔接痕或把熔接痕趕到非外觀面,3個熱射嘴的射膠時間和順序采用順序閥控制,順序閥由油缸的驅(qū)動,其開閉順序和時間由模具智能化系統(tǒng)控制,以得到最優(yōu)的成型質(zhì)量。由于門板表面不能有澆口痕跡,故只能采用“熱流道+冷流道”組合式澆注系統(tǒng),熔體經(jīng)熱流道、冷流道,最后由3個扇形澆口從側(cè)面進入型腔[1-2,7]。澆口位置見圖8,圖中G1、G2和G3為熱射嘴位置。熱射嘴至塑件邊緣的流道長度不宜超過50mm,過長的冷流道會導致熱量及壓力損失過大。
2.4 模具側(cè)向抽芯機構(gòu)設計
側(cè)向分型與抽芯機構(gòu)是本模具最復雜的結(jié)構(gòu)之一。成型塑件存在6個與開模方向不一致的倒扣,其中倒扣S1~S5在塑件外側(cè),模具采用了“滑塊+斜導柱+彈簧擋銷”的側(cè)向抽芯機構(gòu),S6為內(nèi)側(cè)倒扣,倒扣深度10mm,面積較大,模具采用了“斜頂+斜推桿”的內(nèi)側(cè)抽芯機構(gòu)[8]。模具側(cè)向抽芯機構(gòu)詳見圖2(b)、(c)、(e)。S6倒扣抽芯距離較大,為避免成型塑件在側(cè)向抽芯時黏斜頂,導致塑件變形甚至斷裂,側(cè)向加強筋的脫模斜度不得小于2°。另外,由于S6倒扣方向不是和脫模方向垂直,屬于傾斜式內(nèi)側(cè)抽芯,故斜推桿的底座中滑動導軌的方向必須與內(nèi)側(cè)抽芯的傾斜角度一致,即采用傾斜式導滑槽,否則,內(nèi)側(cè)抽芯時加強筋會斷裂,見圖9。
由于成型塑件對斜頂包緊力較大,在汽車左前門板模具斜頂?shù)脑O計中,要防止側(cè)向抽芯時塑件對斜頂?shù)恼尺B,避免斜頂將塑件拉裂。
2.5 模具溫度控制系統(tǒng)設計
成型塑件的冷卻時間占成型周期的80%左右,成型塑件的填充不良和翹曲變形通常都是模具型腔各處的溫度不合理造成的。對于汽車左前門板這種汽車最重要的大型內(nèi)飾件,溫度控制系統(tǒng)設計原則是使模具能夠均衡冷卻和快速冷卻,為此冷卻水道之間的距離必須合理,冷卻水道距離型腔面應大致相等。
根據(jù)以上原則,汽車左前門板模具溫度控制系統(tǒng)動模采用8組冷卻水路,定模采用10組冷卻水路,每條冷卻水路都由直通式水管和隔片式冷卻水井組成,詳見圖10,圖中不同的顏色表示不同的冷卻水路。模具冷卻水路沿型腔等距離布置,縱橫交錯,呈網(wǎng)格狀。冷卻水流動方向與料流方向大致相同,進出水路長度大致相等,水道之間的間距保證在50~60mm之間,冷卻水道距型腔面在20~25mm之間,冷卻水道與推桿、推塊等推件孔保持了至少8mm的距離[9]。本模具定動模設計了網(wǎng)孔鑲件,動、定模網(wǎng)孔鑲件和斜頂都單獨設計一組冷卻水冷卻??焖偾揖獾睦鋮s系統(tǒng)大大提高了成型質(zhì)量和模具的勞動生產(chǎn)率。成型塑件尺寸精度提高了一級,達到了MT3(GB/T14486—2008),注射周期縮短了約8%。
2.6 脫模系統(tǒng)設計
汽車左前門板模具脫模系統(tǒng)包括了推桿、推管、推塊等所有的常規(guī)推出零件,各推件的位置詳見圖11,圖中粉紅色為推管(即司筒),綠色區(qū)域為推塊,紅色的為圓頂針位置。這些推出零件固定在推件固定板11上,推件固定板11由4個頂出油缸18驅(qū)動,其作用是將脫模零件推出并拉回復位,復位的準確度由行程開關(guān)17控制。因為是特大型模具,推件固定板須設計了6支導柱和導套,推件底板下方設計了6個限位釘。定模A板與復位桿接觸的區(qū)域都設計了一塊比復位桿大10mm的回復硬塊,回復硬塊選用油鋼DF2(冷作工具鋼),并經(jīng)淬火熱處理。模具設計了平衡布置的6支限位柱,頂出距離控制在110mm。推桿排布在包緊力大的位置,最大直徑φ20mm。
由于斜頂37須依靠定模A板3推回復位,為了防止二者反復撞擊使定模A板3產(chǎn)生凹陷,從而影響斜頂37復位精度,模具設計了復位桿先復位機構(gòu),即在復位桿的大端下方設計一塊彈力膠27,見圖2(f)。開模后,彈力膠27將復位桿26向前推出4mm,合模時,定模A板3提前4mm接觸到復位桿26,從而提前將斜頂37推回復位,大大減小了斜頂37和定模A板3的撞擊力度。
3 模具排氣系統(tǒng)設計
汽車左前門板體積大,模具在注射成型過程中型腔內(nèi)有大量氣體需要及時排出,若排氣不良,會嚴重影響成型塑件的質(zhì)量,出現(xiàn)填充不良、困氣甚至會燒焦塑件等成型缺陷。另外,成型塑件和型腔接觸面積大,開模時外部氣體必須及時進入型腔,否則就會形成真空,造成黏定模型腔或脫模困難。汽車左前門板注塑模具屬于平板類零件,模具主要通過分型面排氣,分型面上的排氣槽沿型腔布置,由一級排氣槽、二級排氣槽和三級排氣槽組成,排氣槽開設在定模側(cè)的分型面上,詳見圖12。一級排氣槽深度0.04mm,二級排氣槽深度0.5mm,三級排氣槽深度1mm,排氣槽寬度均為10mm。分型面上的排氣槽加工方便,易清理,排氣效果好。
4 模具工作過程
(1)注射充模:熔體依次經(jīng)過一級熱射嘴8、熱流道板5、二級熱射嘴6進入分型面之間的冷流道,最后由扇形澆口進入模具型腔。它分3個階段:流動充模、保壓補料、防止倒流。(2)冷卻定型:在溫度控制系統(tǒng)作用下,熔體冷卻和固化。(3)開模及外側(cè)抽芯:成型塑件固化至足夠剛性后,注塑機驅(qū)動動模開模。在開模過程中,5支斜導柱撥動5個滑塊對成型塑件進行外側(cè)抽芯。開模距離500mm,由注塑機控制。(4)脫模及內(nèi)側(cè)抽芯:注塑機頂出油缸18推動推件固定板11,一邊推動推桿、推管和推塊將成型塑件推離動模,一邊推動斜推桿39及斜頂37進行內(nèi)側(cè)抽芯。(5)合模復位:塑件由機械手取出后,頂出油缸18拉動推件固定板11復位,推出零件及斜推桿最后在復位桿26作用下準確復位,行程開關(guān)17打開,注塑機推動動模合模,模具開始下一次注射成型。
5 結(jié)論
(1)汽車左前門板喇叭網(wǎng)孔成型零件采用粉末冶金透氣鋼,提高了排氣效果,改善了熔體流動,成功消除了喇叭網(wǎng)孔填充不良和熔接痕等成型缺陷。模具采用傾斜式導滑槽,有效解決了傾斜式內(nèi)側(cè)倒扣脫模難題。
(2)模具3個針閥式熱射嘴采用順序閥熱流道智能控制技術(shù)(簡稱SVG),精確控制噴嘴的流量和壓力,成功解決了大型薄壁塑件熔體填充難題,大大提高了成型質(zhì)量。
(3)動、定模共18組水路呈網(wǎng)格狀,縱橫交錯,有效達到了模具型腔各處的溫度平衡,這種溫度控制系統(tǒng)應用效果明顯,注射周期縮短了約8%,尺寸精度達到了MT3(GB/T14486-2008)設計要求。
模具設計思路正確,結(jié)構(gòu)先進合理,對大型、薄壁、精密、長壽命注塑模具設計具有較強的參考價值。模具順利投產(chǎn),運行安全,各項指標均達到設計要求。
參考文獻 :
[1]張維合.注射模具設計實用手冊[M].北京:化學工業(yè)出版社, 2011:112-177.
[2]張維合.汽車注塑模具設計要點與實例[M].北京:化學工業(yè)出版 社,2016:23-45.
[3]萬鵬程.汽車保險杠注射模澆注系統(tǒng)設計與成型參數(shù)優(yōu)化[M].昆明理工大學出版社,2011,58-75.
[4]沈忠良,鄭子軍,肖國華,等.汽車中控面板IMD 成組模具設計 [J]. 工程塑料應用,2017,45(1):70-75.
[5]吳夢陵,Moldfow 模具分析實用教程[M].2 版.北京:電子工業(yè)出版社.2018.
[6]張維合.基于順序閥熱流道技術(shù)汽車導流板注射模設計[J].塑料 科技,2018,46(12):100-105.
劉彥國.塑料成型工藝與模具設計(第4版)[M]. 北京:人民郵電出版社,2018.
[7]周紀委,王明偉.汽車尾門左右窗框飾板氣輔注塑模具設計[J]. 中國塑料,2023,37(11):141-148.
[8]CGLi,Yuguang Wu.Evolutionary optimization of plastic injection mould cooling system layout design[J].IEEE 2010:693-696.
[9]張云.汽車通風管接頭注塑模具設計[J].塑料,2023,52(05): 74-78.
[10]劉祥建,周佳睿,姜勁.基于Moldflow的按鈕開關(guān)帽注塑模具設計[J]. 工程塑料應用,2023(06):97-102.
[11]Ren Jong,W Wu,Ch Liu,et al.A Collaboration NavigationSys- tem for Concurente Mold Design[J].The International Journal of AdvancedManufacturing Technology,2009,40(3/4):215-225.
[12]趙利平,張維合,彭新華,汽車座椅側(cè)護板注塑模具創(chuàng)新設計 [J]. 中國塑料,2023,37(10):139-143.